ARCHITECTURE
The building has 7 floors and underground parking facility on 3 levels. There are 106 apartments, 6 offices and 3 retail units, and a back yard situated in the apartment house.
LOAD-BEARING CONSTRUCTIONS
The building was constructed using monolithic reinforced concrete pillar construction in accordance with the structural engineering report. The structure of the elevator’s perimeter walls is also reinforced concrete.
WALLING
The main cross-walls between the limiting bearing walls and the reinforced concrete pilaster were made of Porotherm burnt masonry material (ceramics). The partition walls between the apartments are brickworks. However, the inner partition walls are partly plasterboard manufactured.
STAIRCASE
The stairscases were made by using monolit concrete in line with the structural engineering report.
SOCKET/BASE
The floor (&ceiling) structure is covered with footstep sound insulation and flap fitting, floating (cement composition) floor screed.
THERMAL INSULATION
The thermal insulation was made of using Heraklit heat-insulating slab on the uppermost garages’ slabs, and polystyrene sheets on the balconies. The thermal insulation of the roof was made of footstep sound proof rock wool thermal insulation. Mineral wool insulation system was built in the frontage in accordance with the findings of the thermotechnical thickness calculation.
SOUND INSULATION
Footstep sound proof insulating layer was built into all intermediate ceilings. A perimeter insulation strip was situated on all edges of the floating base concrete in order to increase the effectiveness of the footfall sound insulation.
PLASTER-WORK
The complete inner plaster-work was made mechanically. The surfaces of the edges and corners were covered with special protection strips in order to maintain the quality. Instead of the traditional plaster-work, special thinner plaster-work method (fairing) was used on the bottom surface of the flat concrete ceilings. The outer patent plaster is rolling-grained mineral plaster. It is a steam line membrane, but also weather-proof and resistant in the long run.
LOCKSMITH’S CONSTRUCTION, BANISTERS
The steel structures’ surfaces were given a coat of paint both in the inner and outer space. The balconies are equipped with steel banisters.
OUTER DOORS AND WINDOWS
The plastic windows and balcony doors have modern white profile and equipped with thermoinsulated glasses. These windows and doors are practically airtight. The windows have tilt & turn function. The street front windows and doors have modern coloured aluminium frame.
INTERNAL DOORS, THE DOORS OF THE COMMON AREA
Fire-resisting steel doors were situated between the garages and the staircases in accordance with the regulation. These doors have coated surface treatment (dressing). The common areas are also equipped with steel doors.
GARAGES, BASEMENT STORAGES
The tile floor of the basement level is cement screed. The steel doors had coated surface treatment (dressing). The storage places can be locked separately.
GROUND FLOOR APARTMENTS
All ground floor level apartments have separated lots (balconies) from the common garden (back yard). These apartments have direct access to the garden.
HALL DOORS OF THE APARTMENTS
The hall doors of the apartments are modern multiple point locking doors equipped with security locks (dead bolts).
BUILDING ENGINEERING
SEWERAGE, DRAINAGE, WATER SUPPLY, HEATING
The building is equipped with PVC sewerage infrastructure with bell-and-flange pipe joints. The rainwater and sewage-water systems are separated. There are no floor drains in the apartments. All the bathrooms are have washing machine and sewage access and wall hidden toilet tanks. The bathrooms are equipped with tubs or showers dependent on the apartment structures.
Service warm water is ensured by the building’s own central condensation boiler and supply system. This boiler house also ensures the heating services of the building. Each apartment’s bathroom is equipped with it’s own calori-, and water-meter.
Hot water is also utilized to for the heating of the apartments (radiators). The heating bodies are with steel plate heaters in the bathrooms (towel dryer type). The radiators have thermostatic valves. There are “Alföldi” sanitary installations, “Kludi” tap installations and “Zalakerámia” quarries constructed in the bathrooms.
VENTILLATION
The ventilation is based on gravity system. However, the inner spaces also have forced ventilation (central exhaust bowler).
ELEVATOR
Both staircases have one modern elevator without engine-house. The operation of the elevators are quiet and have low maintenance costs.
ELECTRICITY, HEAVY CURRENT SYSTEM
The complete electric network in the apartments is inside the walls. The copper conductor system is protected with shield tubes and covered with the necessary protective grounding.
Every room is equipped with electric socket (230 V) in accordance with the electrical planning documentation. Each apartment has outer lockable meter boxes located in the stair hall. The common areas were equipped with lamp armature.
DOOR CALLING SYSTEM
The access through the staircase doors is secured by an intelligent door calling system. The admission (opening the front door) is controlled from the apartments. The lockable letterboxes are located in the staircases, next to the front door.
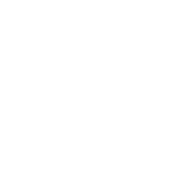